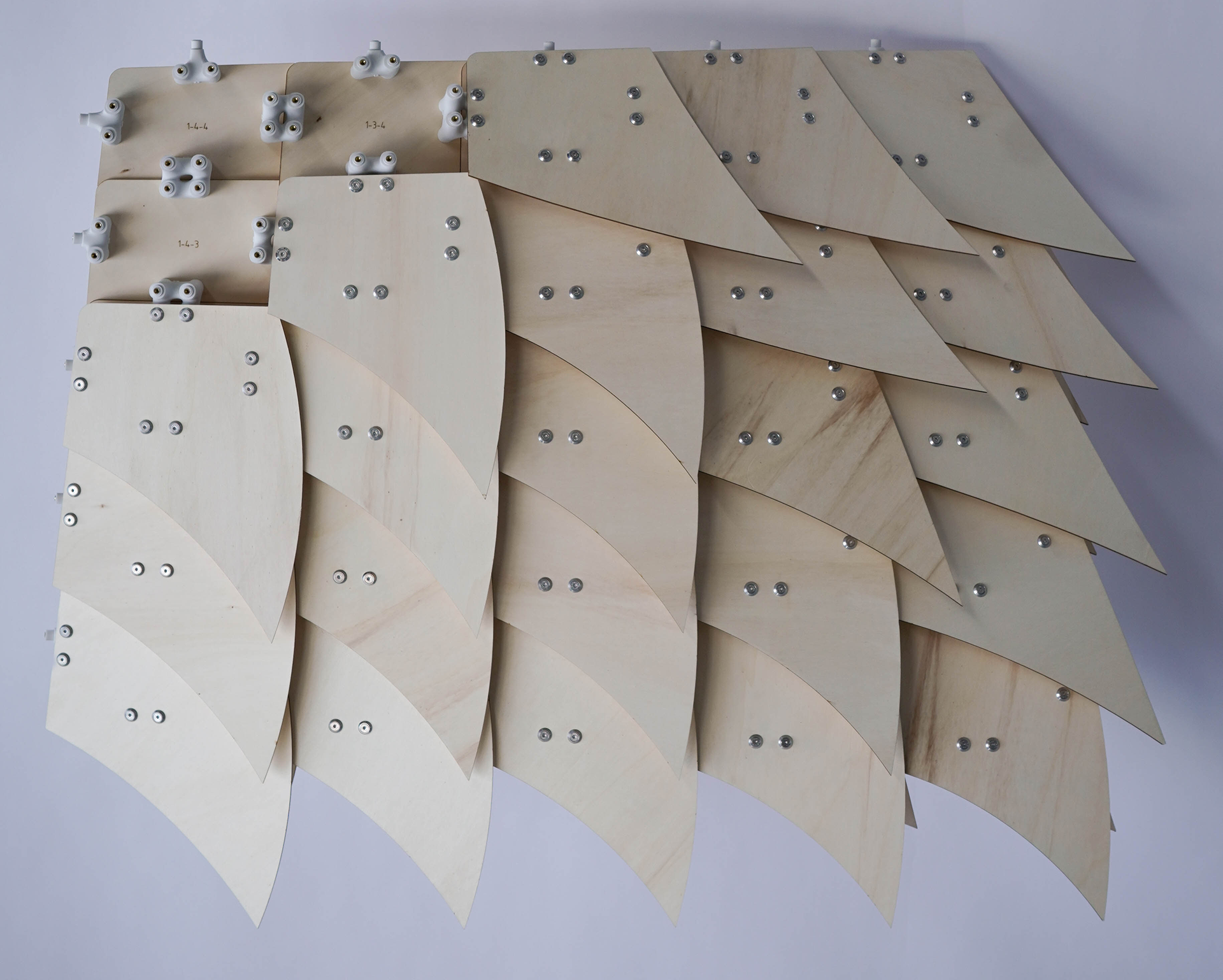
Im Rahmen des Kurses Space Shingles wurde das Universal Joint Projekt weiterentwickelt. Dieses Projekt kombiniert moderne Technologie, fortschrittliches Design und Funktionalität, um die Potenziale architektonischer Gestaltung zu erweitern.
Die Idee hinter den Space Shingles besteht darin, eine parametrische und ästhetische Hülle zu schaffen. Hierfür wurden parametrisch gestaltete Schindeln (Shingles) und Verbindungsknoten kombiniert. Die Verbindungsknoten wurden mittels 3D-Druck präzise hergestellt, während die Shingles durch Laserschneiden eine akkurate Form erhielten.
Die Stabilität und Flexibilität der Space Shingles werden durch die Integration von Gewinden in die 3D-gedruckten Knoten gewährleistet. Diese ermöglichen eine effiziente Befestigung der Platten, um eine widerstandsfähige Hülle zu schaffen. Die Knoten können mit ihrer parametrischen Struktur eine hohe geometrische Freiheit ermöglichen.
Besonders bemerkenswert ist die Formgestaltung der Platten, die eine Tropfkante ausbilden, um den Wasserabfluss zu optimieren.
Um die Leistungsfähigkeit der Space Shingles unter verschiedenen Witterungsbedingungen zu überprüfen, wurde eine Wassersimulation durchgeführt, die die Effektivität des Designs bestätigte.
Die Anwendungsmöglichkeiten der Space Shingles sind vielfältig und reichen von modernen Wohngebäuden bis zu öffentlichen Strukturen mit futuristischem Ansatz.
Insgesamt verkörpern die Space Shingles das Potenzial digitaler Methoden und 3D-Drucktechnologie für innovative Lösungen im Bereich der Architektur.
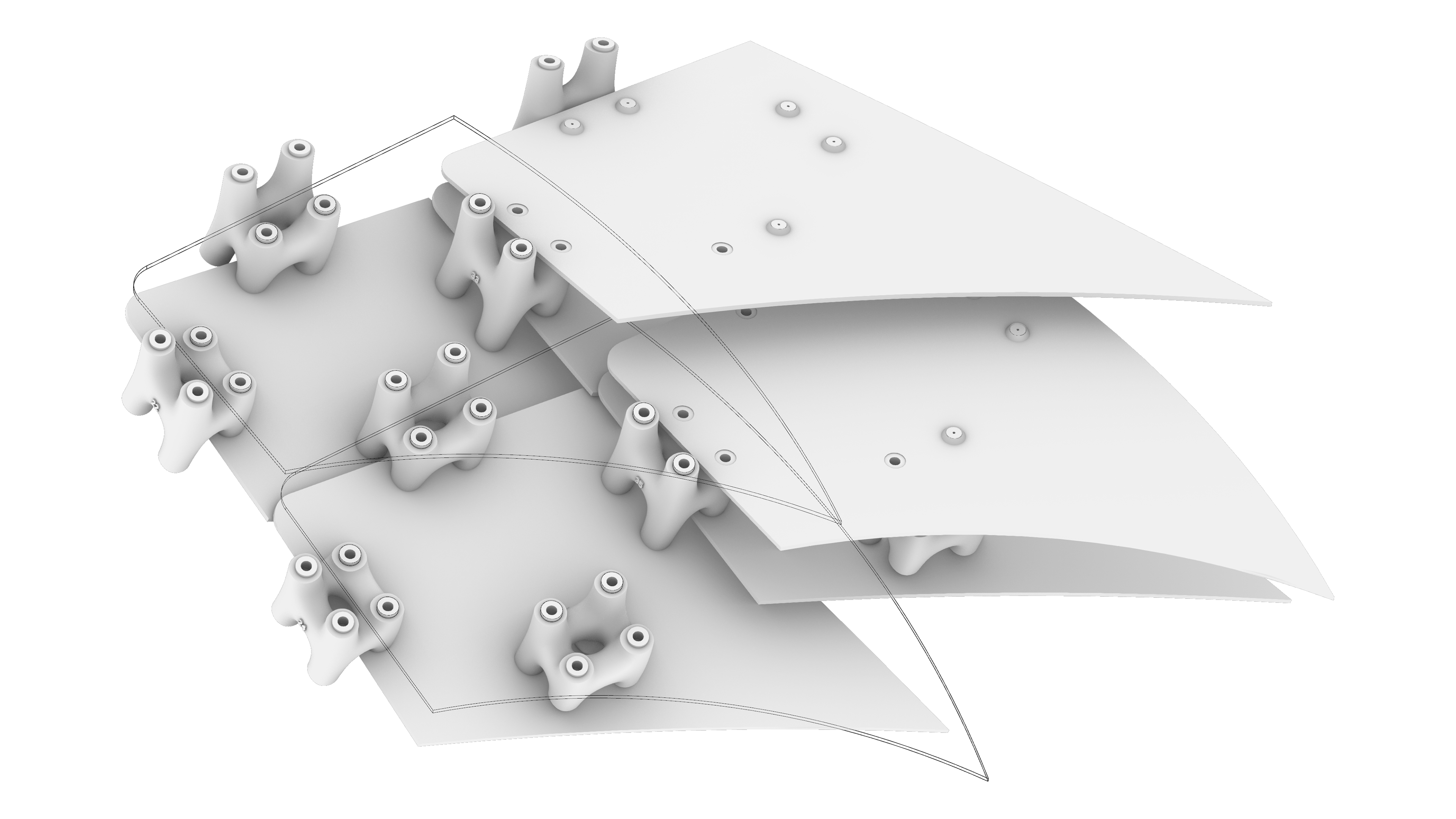
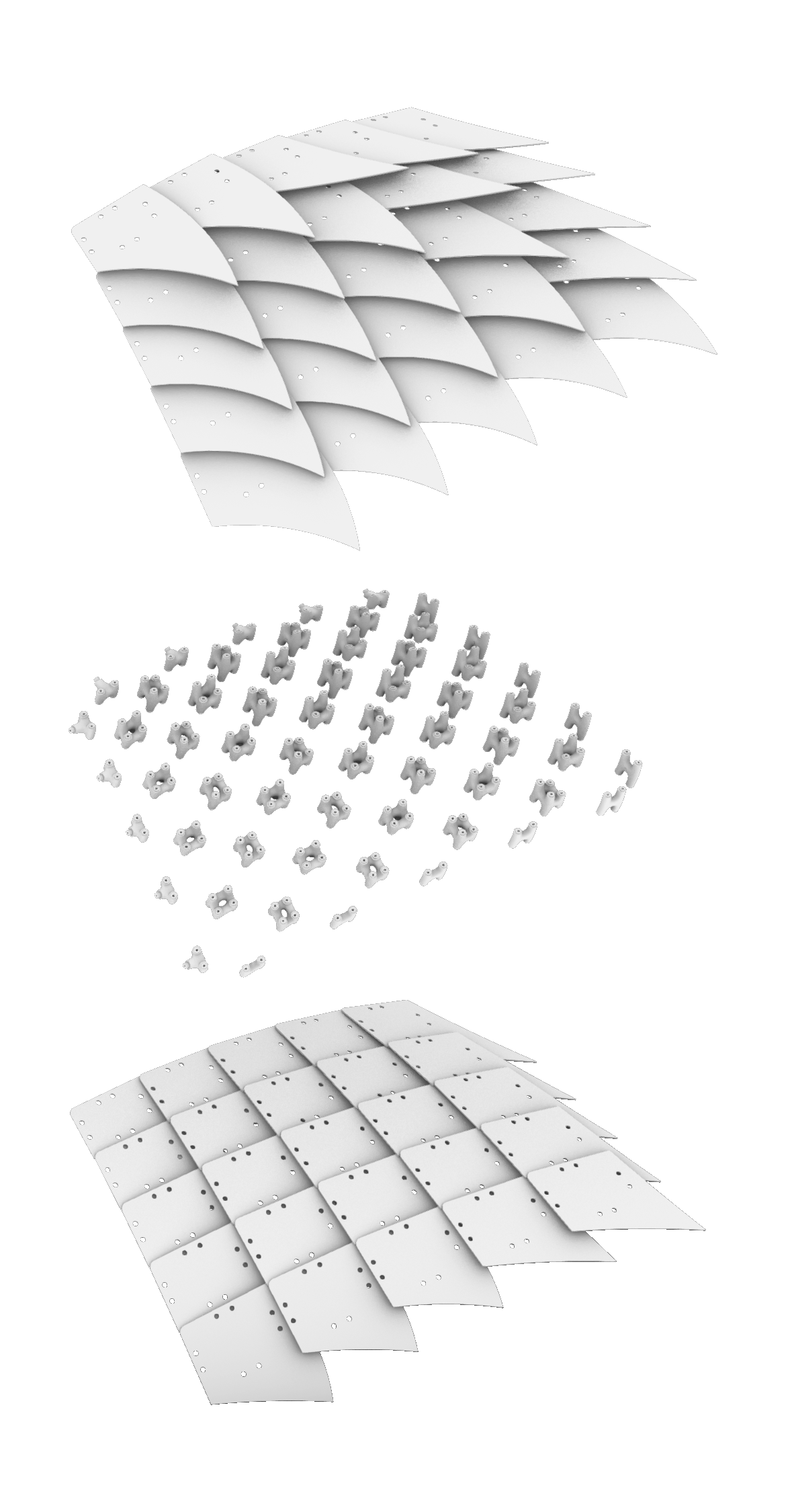
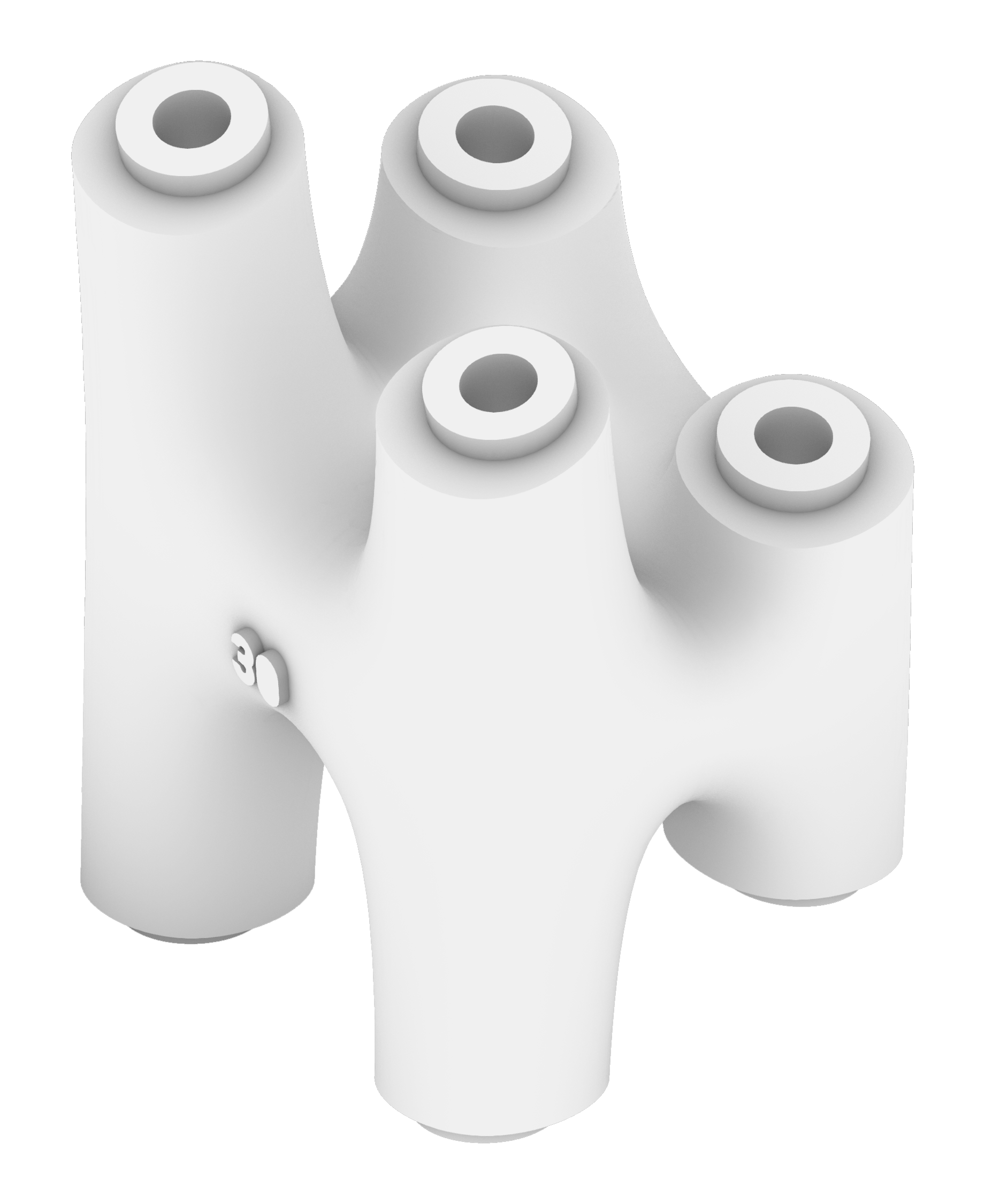
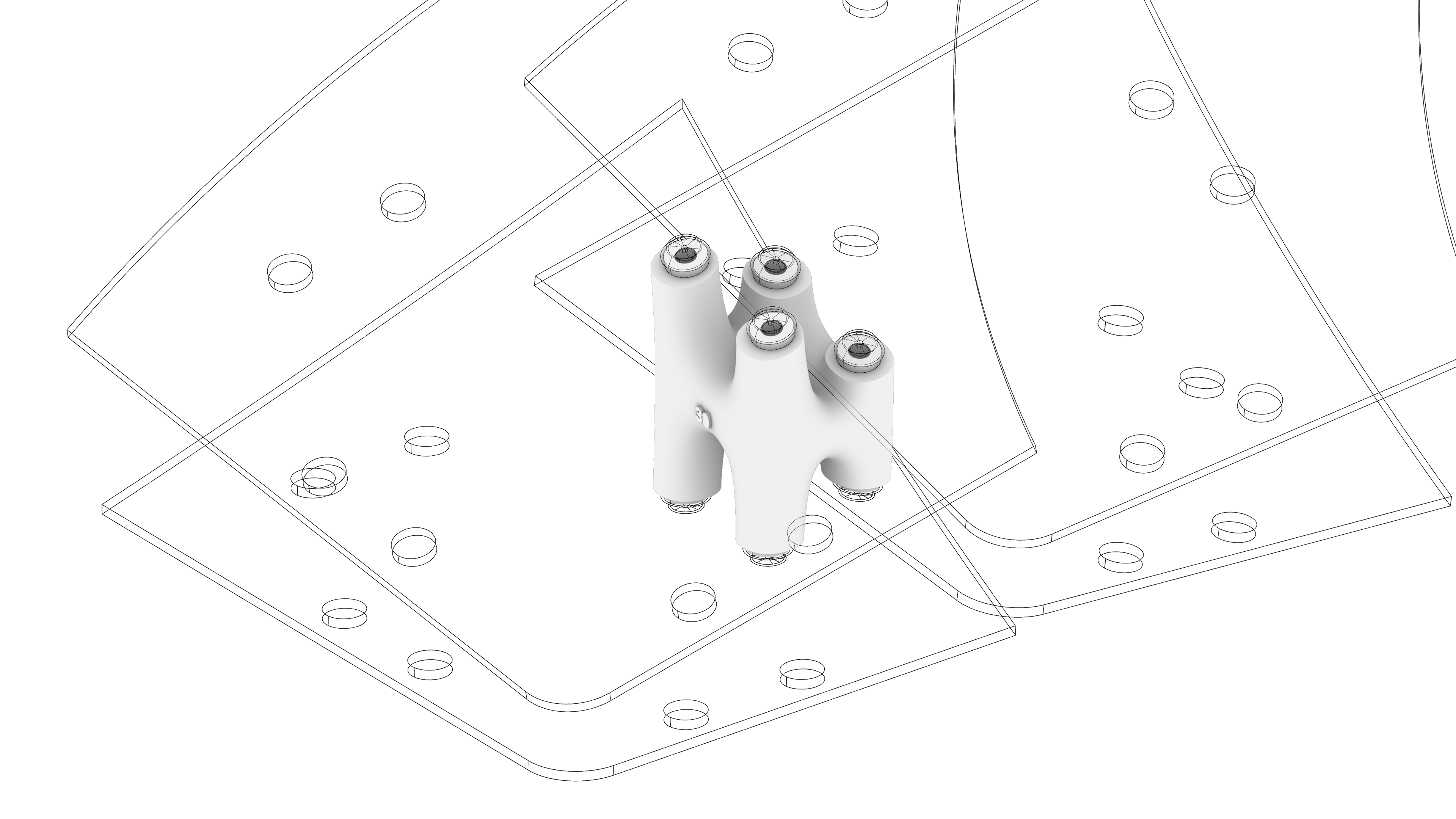
Space Shingles II
Die Fortsetzung des Kurses im Folgesemester baute stark auf den vorangegangenen Erkenntnissen und Kompetenzen auf. Dieses Mal lag das Augenmerk der weitmöglichsten Optimierung nicht wie im ersten Teil auf den Schindeln, sondern auf den Knotenpunkten selbst.
Die Knotenpunkte wurden nach Berechnung der einwirkenden Kräfte auf Steifigkeit und Materialverbrauch optimiert. Um den Kraftverlauf für die Simulation korrekt anzugeben, werden an allen acht Haltepunkten pro Knoten die anliegenden Kräfte, welche durch die Schraube und die Gewinde in den Knoten übertragen werden, berechnet.
Diese Daten werden dann bei der Formoptimierung als Grundlage gewählt und schaffen so einen Knoten mit der kleinstmöglichen Oberfläche. Durch eine Finite-Elemente-Berechnung werden, die am wenigsten beanspruchten Teile des Knoten wegoptimiert.
Aber das ist nur die erste Hälfte der Optimierung dieser Hochleistungsknoten.
Im nächsten Arbeitsschritt wird erneut der Kräfteverlauf im Bauteil ermittelt und nach dem Kraftmuster eine Lattice-Struktur im Knoten verlegt. Durch die dadurch entstehenden Hohlräume wird weiter Material und somit Gewicht gespart, ohne dabei die Tragfähigkeit erheblich einzuschränken.
Mit der Pulverdruckmethode kann so das überschüssige Material entfernt und wieder verwendet werden. Damit haben wir einen leistungsstarken und nachhaltigen Verbindungsknoten geschaffen.
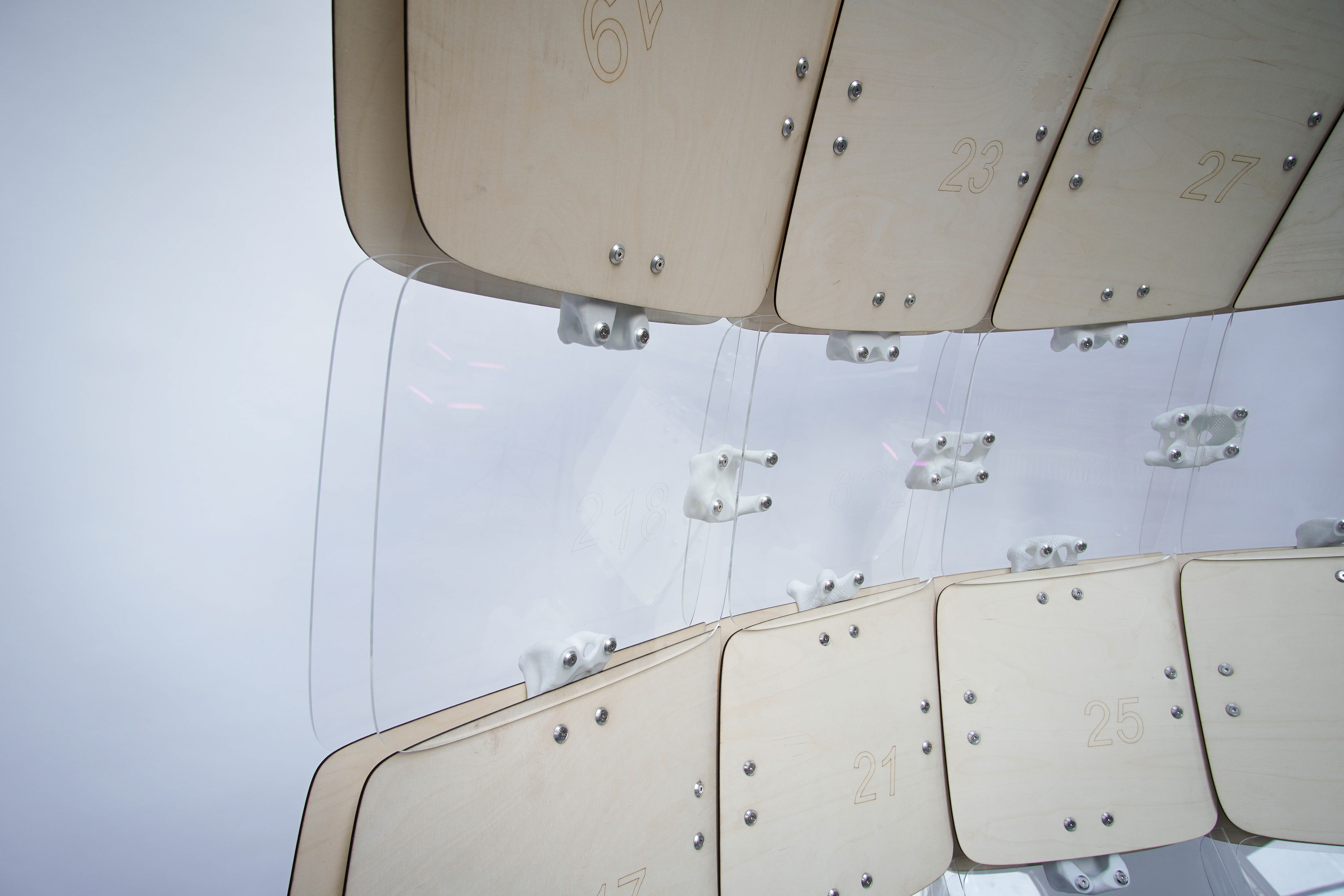
Jahr: 2020/2021 | Ort: Hannover
Institut für Gestaltung und Darstellung
Abteilung digitale Methoden
Dozent: Philipp Mecke
Institut für Gestaltung und Darstellung
Abteilung digitale Methoden
Dozent: Philipp Mecke